The manufacturing industry has existed for more than a century and has time-tested processes. Today, this industry is officially in the age of Internet of Things (IoT) adoption. As discussed in a white paper by Schneider Electric, this change should be seen as an evolution, not a revolution. Companies have invested hundreds of millions in industrial automation and control systems and are often unwilling to invest hundreds of millions more to replace those systems with new technologies.
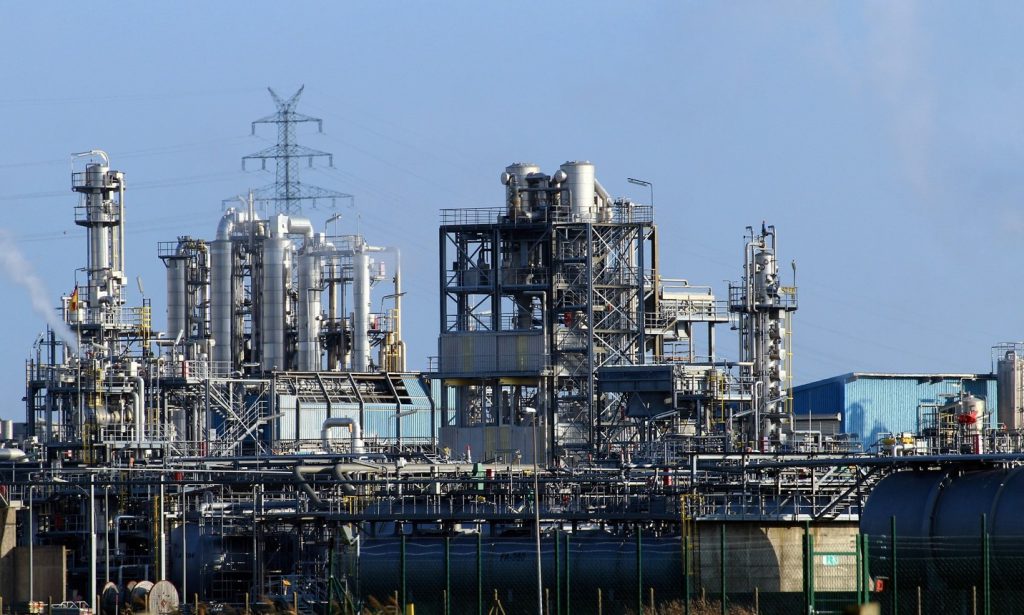
There is a need to leverage modern technologies to accommodate changing conditions. Overall, the industry is understanding this need in order to keep up with changing times, to optimize their processes, to increase operational efficiency, and to deliver good experiences to customers.
Some companies are motivated to invest in IoT technology to comply with government regulations, such as monitoring pollution and providing live data. Any failure to meet these regulations can be lethal, as it can lead to the company’s license being revoked. Considering these circumstances, Internet of Things has emerged as a new technology that helps improve processes by providing automation, control, and efficiency, thereby saving time and money.
However, adopting IoT in this industry has many challenges, especially in developing countries. These challenges range from the employees and their awareness of technological products to the manufacturing environment of existing industry practices. Manufacturing plants are often located in rural or semi-urban regions away from cities. And most of their non-management employees, such as operators and floor managers, live in close-by villages and towns. The Internet has touched their lives; however, the use of the Internet is still limited to communication and entertainment.
Using the Internet to integrate IoT-enabled devices for purposes that have higher stakes—such as in an industrial plant—is still a novel practice for these companies and sometimes involves applying traditional methods for the practice to gain acceptance. As technology adoption in manufacturing increases, the growing skills gap is also becoming increasingly apparent.
Challenges in this Space
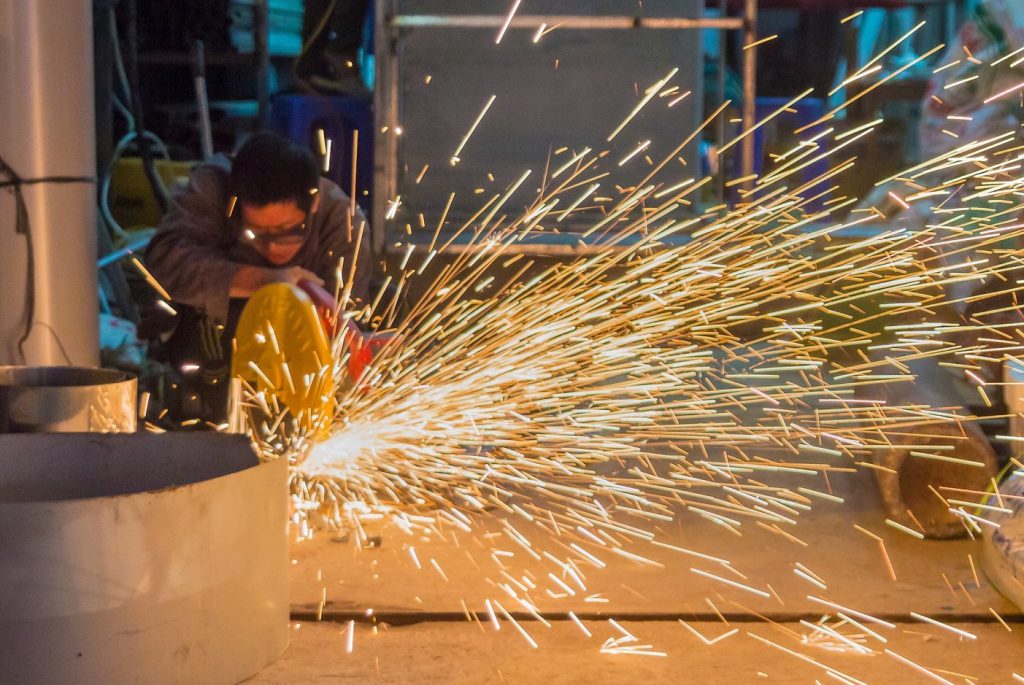
When companies began making IoT based software products for the manufacturing industry, they started facing many challenges—for example, lower user adoption and users abandoning the product after the purchase. This created a desire to understand the reasons for these behaviors and to find solutions to fix them.
This industry also has multinational corporations that are working toward cost savings through automation. These corporations also have big budgets for training and experimentation. In the same market, there are owner-based companies or small and medium enterprises (SMEs) with smaller budgets that do not wish to invest in intensive digitalization for their manual practices, and subsequently do not train their employees in the adoption of the IoT. However, these companies may be forced to take this route due to government regulations.
In the paper “Cultural Barriers in the Adoption of Emerging Technologies,” the authors assert that SMEs that are likely to adopt new IT usually have a CEO who has a positive attitude toward innovative technology and is knowledgeable about IT. However, even this group struggles with technologically unskilled employees. Thus, while designing an enterprise product for a desktop or mobile app, it is important to discuss the challenges in adopting IoT technologies for this user group.
Product-Based Challenges
The challenge begins right after the purchase of the product: from installation of the product, getting started, day-to-day usage, and calling customer care and resolving issues to periodically upgrading the software. The following are the top challenges in adopting technology for this user group:
- Environment: Some small-scale manufacturing companies do not have or have limited access to the Internet in their plants. This makes it difficult to download large files or to engage in live chat sessions with customer support. After installation, poor Internet connectivity may make the system unstable, requiring constant human intervention.
- Installation: Software installations are complex, as they require defining many parameters unique to the plant and government regulations for that particular industry. In addition, there is often no specific role of an IT admin in some manufacturing plants. Many times the individual responsible for installing and using the software may perform many roles related to plant management. This person often comes from a manufacturing background and is not trained in the complexities of IT or the installation of plant software. Therefore, close assistance or help for installation of the software is required.
- Getting started: Enterprise software often lacks a good onboarding experience to help users learn about the product. The importance of using a digital product versus previous approaches may not be communicated by management. What little learning material is available is often in text-heavy documentation that is hidden under layers of a UI. This causes user frustration and lowers motivation to invest time to learn about and use the product.
- Day-to-day usage: Because companies often use complex interfaces and terminology that is for power users such as IT admins, when users start to use the product, they are often unable to discover features that are hidden in complex navigation, and are burdened with unfamiliar concepts such as reporting dashboards or configuring settings.
- Upgrading software: Software builds are constantly evolving. New versions need to be downloaded, and systems need to be upgraded. Going online, downloading, and upgrading the working system can create a fear in users that a change may break down the mission-critical software.
- Trust: For ages, companies have been using manual systems; trusting that a machine can give reliable information requires a significant mindset shift. At the same time, these systems are evolving, so they are subject to errors and system failures. This adds to the existing distrust of a system.
Language-Based Challenges
Language also plays a vital role in learning and adopting these systems. Documentation and support are often provided in English only; we need to remember that in several countries English is used for only official work. English-educated users within the same organization can use it effortlessly, but there is another group of workers in the field who have difficulty comprehending it. Most on-the-ground workers have a limited understanding of English and can read only regional languages, but much of the documentation and software produced by industries are typically in English. This makes it harder for users to read documentation, follow instructions, and to seek help. This leads to many problems, including higher support calls that require customer support representatives who speak the local language to help resolve issues.
Importance of UX Research in the Manufacturing Space
In order to create effective software for this population, we need to create products based on an understanding of the users’ needs and constraints. Therefore, user research is critical.
There are two important factors to this issue. First, user research helps identify all kinds of users, both primary and secondary. Second, users play a very important role in performing tasks, as well as planning time and resource management. After identifying user types, a strategic research approach needs to be designed to gain user insights. User profiles assigned by product managers often focus on primary users only, as they focus on product usage without considering alternative manual approaches. Thus, educating internal teams becomes a part of the research strategy to help them take a more holistic view. Transparency and trust are critical to get information from the teams.
Conducting the Research
When conducting research for an IoT-based software product that is used by industrial plants, it is very important to understand all types of users, their roles, responsibilities, and how they are associated with the product.
Data Collection
User groups can vary from power users to users who might be only using a basic Android phone for limited operations. In a blog post by Dr. Rishi Bhatnagar, chairperson of the Institution of Engineering and Technology—IoT Panel for India, he noted that “IoT requires multidisciplinary skillsets and a combination of domain knowledge, which is scarce in current workforce.” Therefore, it becomes critical to identify and recruit the right participants.
Furthermore, within the company it is important to study the employees in customer-facing roles and to gain an understanding about their challenges and their perspectives on the challenges for their users. Overall participants should be both internal and external:
- Internal refers to customer-facing employees, like product managers, sales teams, and customer support.
- External refers to all kinds of stakeholders, from end users (who use and maintain IoT enabled devices) to the purchasing manager, the IT admin, and so on.
Process
The study should start with gathering information to understand internal stakeholders’ goals and perceptions. The next phase should be about gaining insights about the end users to help form the research strategy. These insights will help determine the best method to use, what usability metrics should be used, and so on.
Phase 1: Research with internal stakeholders.
Before meeting with end users, it is important to understand the needs of the internal team. This involves identifying all the internal stakeholders and studying the hurdles they face with their customers. The research method can use a mixed approach by using in-person interviews, listening to customer support center calls, and attending a few sales sessions with the sales team.
Phase 2: Meet with users.
There are two groups of users: One is management and the other is the workers. The first group is from the top management that might be focused on getting high-level information to see how the plant is doing and how efficient workers are. The information gathered during this phase will help these top managers optimize the company to produce a better product.
For the second group of users, the plant workers, getting insights from this group needs to be carefully planned, using designed questionnaires and scripts. It is very important not to rely on self-reported user feedback but to validate as much as possible by visiting physical worksites and observing how people work. The following are a few methods that work particularly well with these types of users:
- Interviews: Speak with management users; they are the people who have defined measurable goals for the organization and therefore drive product adoption. Beginning the study by getting insights from this group is a good starting point. The information gathered during these interviews will highlight issues such as the company’s perception about users’ challenges and will also help to inform on-field strategies.
- Contextual inquiries: This later stage involves visiting users in their environment, such as visiting factories and studying workers and management while they are using the product. During these sessions, users are asked questions and then observed while they work in their own environment.
- Diary study: While studying employees once at work in the plant can provide information concerning usability challenges, this one-time observation will not expose their day-to-day usage, how they learn to use their tools, and the challenges they face producing a product. To get more insight on these aspects, a couple of weeks of study can help provide this necessary information. One important tool to record this insight is the use of a diary. During the contextual inquiry sessions, you may consider asking employees to submit a diary for the study. The employees could submit entries daily using a program like WhatsApp. Entries could include pictures, videos, or audio recordings because simply typing their submissions may be considered tiresome, discouraging this user group from submitting entries.
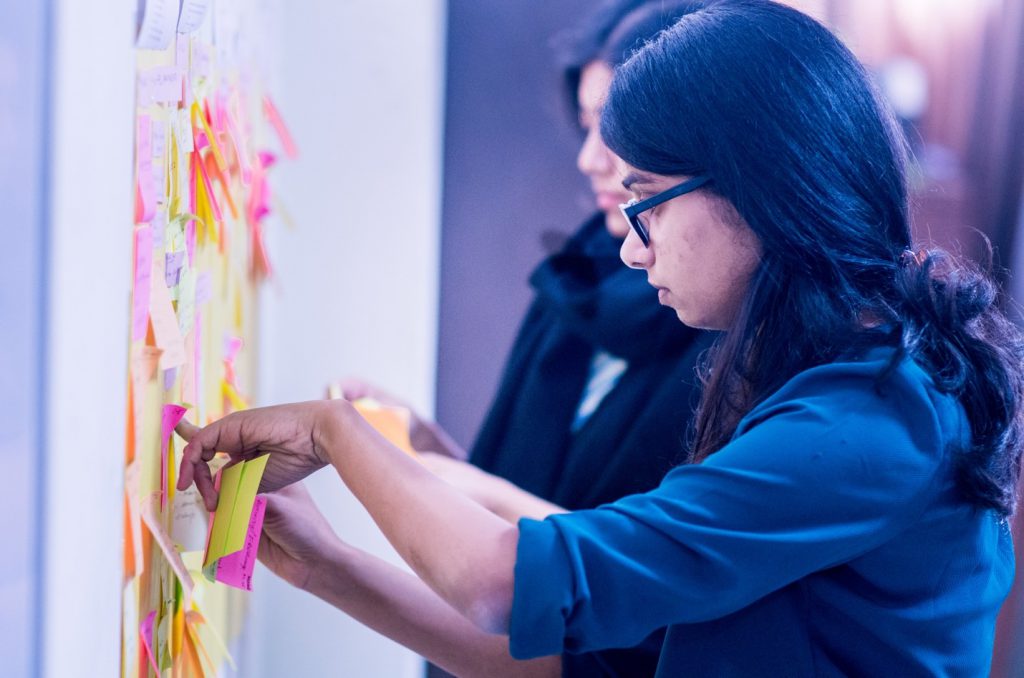
Findings
The findings report should include a variety of insights, including feedback from top management, limitations of customer support and sales, design/usability issues, and other insights. Therefore, it is important to include both a high-level summary for everyone and department-specific detailed reports that can be presented to each stakeholder group. There should be a way to track the changes and the criticality of the issues in each relevant department. It helps for teams to understand what is lacking in which department and who is working toward fixing it.
Summary
The benefits of IoT adoption for the manufacturing industry are significant. However, the rate of growth is still low, and only 30% of manufacturers are investing in digital transformation, while the rest are held back by outdated business models and technology.
Therefore, designers have an opportunity to create solutions that can address these challenges. User research can be the first step to enable teams to get insights to change the product strategy and improve the user experience with a product. For workers, implementing a new technology creates significant challenges as they adapt to a new way of working. As researchers and designers, we can help create products that facilitate better working conditions and provide more accessible technology for a less privileged section of the world.
Anjeli Singh is a UX researcher and entrepreneur. She runs a UX research agency based out of India, called Hureo. At the agency, she is leading various user research projects to highlight the importance of users' insights and is evangelizing the need for user research, usability testing, and, more importantly, the necessity of learning to empathize with users. Before opening the agency, she had worked in companies like Google, Kodak, and Symantec. She has written many articles and has spoken at various conferences including CHI and INTERACT. Twitter: @SinghAnjeli